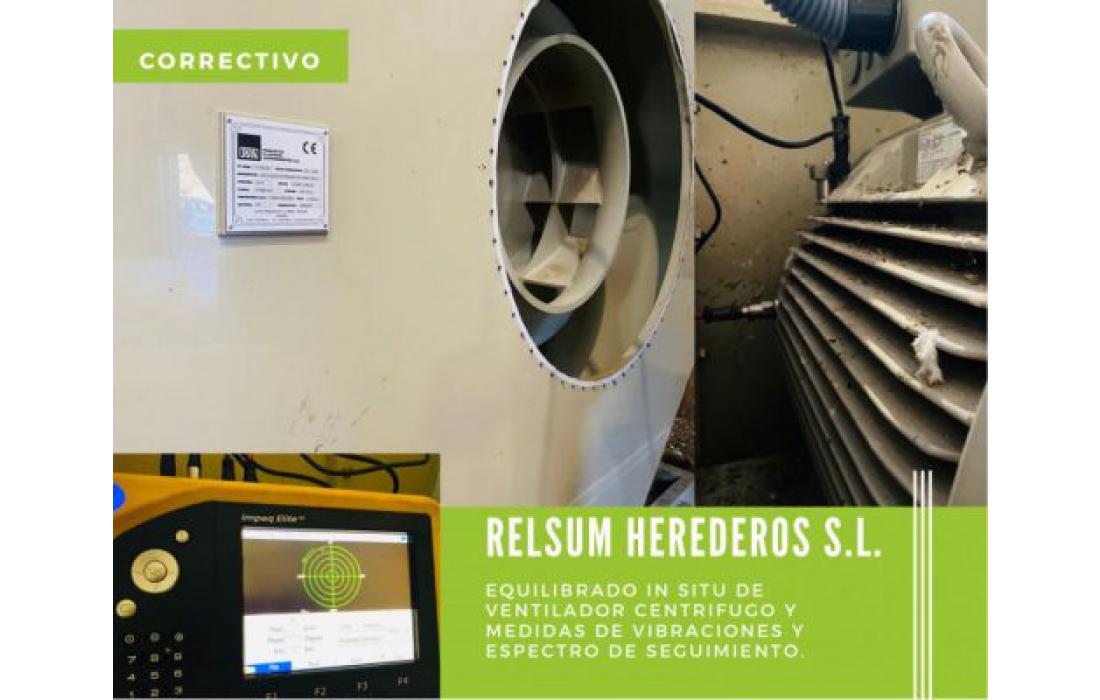
New News
Predictive diagnostics use the signal recorded by data collection equipment, translating mechanical oscillations into a technical language used by machine diagnosticians.
Vibration analyses are based on multiple parameters, the most common of which are frequencies (indicating the mechanical focus or origin), amplitudes (indicating severity), trend (representing the evolution of a localised defect) and vibration pattern (a mixture of several events that an expert takes into account to determine the degree of deterioration of a defect).
On the other hand, as a result of the diagnostics, interventions such as coupling alignment or on-site balancing, resulting from a deterioration or an intervention of one of the replaced components after detecting an anomalous behaviour in operation, are estimated.
Engineers from Relsum's technical department carried out various adjustments on the machines assigned by the customer using the following equipment:
- 5D COUPLING LASER ALIGNER
- MODEL HAMAR LASER 680
- LASER AND REPTOR 680
- CALIBRATED GAUGES
The following software was used for the subsequent data analysis:
- Isee Machine inspection software (comparative analysis in frequencies).
- Couple 6 advancedaligment software.
- Balance Report software.
After the alignments, the performance of the equipment is significantly improved.
Balance Report software.
After the alignments, the performance of the equipment is significantly improved.
Taking into account the maximum speed of 1000 rpm of the motor, the final residual deviation is considered to be the optimum for correct operation.
By reducing the deviation in the couplings, the performance and reliability of the unit is increased, avoiding unnecessary overloads on bearings and other components.